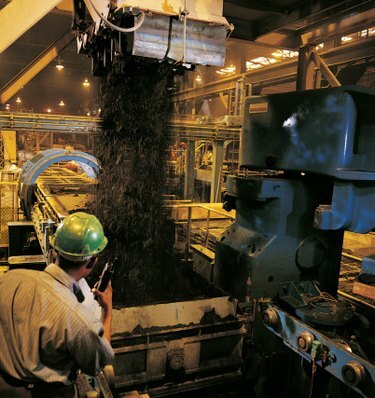
Kompresijsko oblikovanje je najbolj primerno za množično proizvodnjo preprostih modelov.
Kompresijsko oblikovanje je postopek nanašanja toplote na osnovno plastično smolo z uporabo hidravličnega tlaka za ustvarjanje osnovne oblike. To se zgodi, ko toplota stopi smolo in kasnejši pritisk sili temprano tekočino v določen kalup. Ta postopek poteka v kompresijskem kalupu in se tradicionalno uporablja za oblikovanje termoreaktivnih materialov. Ti tvorijo začetno smolo ali tekočino, vendar njihove lastnosti narekujejo, da jih, ko se strdijo in strdijo s postopkom kompresijskega oblikovanja, ni mogoče ponastaviti.
Neprimeren za kompleksne modele
Medtem ko obstajajo tri osnovne vrste kalupov, ki se uporabljajo pri kompresijskem oblikovanju (flash, pozitivni in polpozitivni), nobeden od teh ni primeren za zapleteno ali zapleteno oblikovanje delov. Zaradi zapletenosti vključenih procesov morajo kalupi ostati enostavni za delovanje. To povzroča omejitve izdelkov, ki jih lahko ustvari plesen. Kalupi so zgodovinsko usmerjeni v preproste oblike in množično proizvodnjo.
Video dneva
Nizka stroškovna učinkovitost

Kompresijsko oblikovanje spremeni smolo v toge oblike.
Zaradi odločne narave materiala, ki se običajno uporablja za kompresijsko oblikovanje, to ni posebej stroškovno učinkovit postopek. Glavna težava je, da je termoreaktivni material tog, ko se strdi, in ga zato ni mogoče stopiti v primeru zavrženih ali nezadovoljivih delov. V tem primeru ni mogoče popraviti ali ponovno obdelati nobene manjše napake na oblikovanem predmetu, ta dejavnik pa je neposredno odgovoren za izgubo denarja, materiala, časa in dela.
Poškodbe
Nekatere komponente v kompresijskem kalupu so ranljive in dovzetne za zlom, ko se končni izdelek odstrani iz opreme. Ejektorski zatič je ena takih komponent, ki se nahaja na dnu kalupa. Ko hidravlična stiskalnica v kalupu stisne plastiko, bo izvrgla končni izdelek in to se ponovi vsakič, ko se postopek izvede. Takšna ponavljajoča se uporaba lahko privede do obrabe in na koncu do okvare sestavnega dela.
Trajanje postopka
Cikel postopka stiskanja lahko traja od ene do šest minut, odvisno od izdelka in zahtevane končne obdelave. Običajno cikel traja od tri do štiri minute, zaradi česar je bolj zamuden kot brizganje. Povprečni cikel brizganja je približno dve minuti, v primeru množične proizvodnje posameznega izdelka pa je lahko pomemben dejavnik čas.