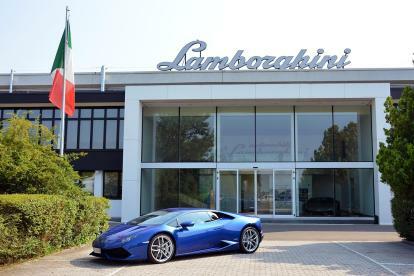
Los robots se están apoderando de las fábricas de automóviles en todo el mundo, pero en Sant'Agata Bolognese, Italia, Lamborghini se está moviendo en la dirección opuesta.
Lamborghini es conocido en todo el mundo por su lenguaje de diseño de vanguardia y su automóvil de última generación. tecnología, pero como descubrimos, el proceso de construcción de un Lambo tiene menos que ver con robots futuristas que con nosotros. pensamiento. En cambio, el fabricante de automóviles de lujo utiliza técnicas artesanales perfeccionadas (y humanas). Únase a nosotros mientras recorremos la planta de la empresa en Sant'Agata Bolognese, Italia, para descubrir cómo se construye un Lamborghini.
Sant’Agata Bolognese es una pequeña ciudad situada a unos 32 kilómetros de Bolonia y a un paso de Maranello, donde Su antiguo rival Ferrari tiene su sede. Mientras Maranello se ha ido transformando poco a poco en una tierra de Ferrari orientada al turismo De alguna manera, Sant'Agata se ha mantenido auténtica a lo largo de los años. Eso no quiere decir que no atraiga turistas, pero hay muy pocos indicios de que sea el hogar de uno de los fabricantes de automóviles deportivos más conocidos del mundo.
La familia Lamborghini
Los empleados de Lamborghini trabajan de 8 a. m. a 5 p. m. de lunes a viernes, aunque la cercana planta de fibra de carbono opera tres turnos para satisfacer la alta demanda. Son fácilmente identificables en Sant'Agata porque visten un uniforme Lamborghini negro que indica claramente si son trabajadores de la línea de montaje, parte del equipo de logística de la fábrica, asignados a la división de construcción de prototipos, u otra persona enteramente.
Relacionado
- Lamborghini Huracán Evo Spyder 2020 revelado antes del Salón del Automóvil de Ginebra 2019
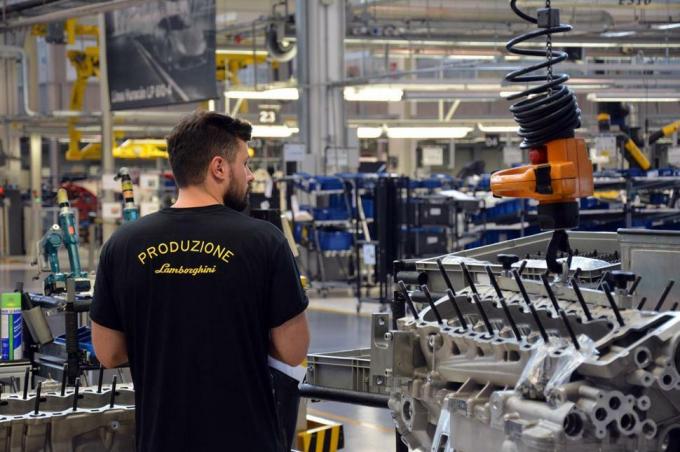
Lamborghini capacita a todos sus trabajadores internamente y se anima a los empleados a pasar de una estación a otra una vez que dominan una determinada habilidad. Por ejemplo, un trabajador que ensambla puertas Huracán hoy podría estar instalando cilindros maestros Aventador dentro de seis meses. Una vez que un trabajador ha pasado suficiente tiempo en la fábrica para conocer Lamborghinis por dentro y por fuera, es elegible para convertirse en uno de los conductores de pruebas de la empresa.
Precisión a través de la artesanía
La parte más impresionante de recorrer la fábrica es ver cómo se ensamblan los coches a mano. De hecho, sólo hay dos robots en toda la planta, una máquina que deja caer las carrocerías desnudas en la línea de montaje y un asador que pone los coches boca abajo cuando es necesario. Como resultado, la fábrica es mucho más silenciosa y espaciosa de lo que la mayoría de la gente imagina.
Cada Lamborghini construido desde 1963 ha sido probado en las pintorescas carreteras de Sant'Agata.
Las carrocerías y paneles de carrocería llegan a fábrica prepintados y envueltos en una lámina protectora de plástico. El Huracán está pintado por la empresa matriz Audi en Neckarsulm, Alemania, porque está construido con más aluminio que fibra de carbono, y El Aventador está pintado por una empresa italiana llamada Imperiale que asigna un solo trabajador a cada coche por el bien de consistencia. Lo primero que debe hacer una vez retirada la lámina de plástico es instalar inmediatamente cubiertas gruesas. para garantizar que la pintura no se raye ni se dañe de otro modo a medida que el automóvil pasa por el ensamblaje línea.
De principio a fin, el Aventador pasa 90 minutos en 12 estaciones diferentes mientras que el Huracán pasa 40 minutos en 23 estaciones. Cada uno está construido en una línea de montaje separada, y una pantalla ubicada encima de cada estación realiza un seguimiento de cuánto tiempo ha estado allí el automóvil, lo que ayuda a los trabajadores a administrar su tiempo de manera más eficiente.
Lamborghini no tiene fundición, por lo que los motores de 10 y 12 cilindros de altas revoluciones que impulsan sus coches son fabricados por proveedores externos y enviados a la fábrica donde se ensamblan (nuevamente, completamente a mano) y probado en banco. Un taller de tapicería fabrica cada parte del interior, incluidos los asientos, los refuerzos para las rodillas y los paneles de las puertas. En el otro extremo de la tienda, un stand especial capaz de replicar una amplia gama de diferentes condiciones de iluminación ayuda a garantizar que la tienda de cuero y Los paneles tapizados en Alcántara que se unen para formar el interior de un automóvil específico son del mismo color independientemente de la cantidad de luz a la que esté expuesto. antemano. Las piezas interiores sólo se envían a la línea de montaje para su instalación una vez que han superado esta prueba.
1 de 28
Cuando un coche está terminado, tiene que pasar por tres rondas de pruebas finales antes de ser entregado a su nuevo y afortunado propietario. La primera ronda implica el uso de láseres y cámaras para comprobar que cada pieza (incluidas las piezas relacionadas con la suspensión y los paneles de la carrocería) esté alineada con precisión. El segundo paso consiste en hacer funcionar el coche en una banco de pruebas (una cinta de correr para vehículos) durante 40 minutos a una velocidad máxima de 180 km/h (aproximadamente 112 mph) para garantizar que todos los componentes mecánicos estén en funcionamiento. Finalmente, el tercer paso es una prueba de manejo completa de 20 a 30 millas en vías públicas.
La tradición es fuerte en Lamborghini y cada uno de los automóviles fabricados en Sant'Agata desde 1963 ha sido probado en las pintorescas carreteras que rodean la fábrica. A pesar de eso, los lugareños de todas las edades siguen volviendo la cabeza cada vez que pasa un Toro Salvaje que escupe fuego.
Recomendaciones de los editores
- Lamborghini está poniendo coches de carreras en tu salón. Súbete y conduce uno
Mejora tu estilo de vidaDigital Trends ayuda a los lectores a mantenerse al tanto del vertiginoso mundo de la tecnología con las últimas noticias, reseñas divertidas de productos, editoriales interesantes y adelantos únicos.